Contact US 🤙+91-990970058, 🤙🤙+91-7420804059 🇮🇳 ✉️info@softwellautomation.com
Advanced Mitsubishi Automation Training
Softwell Automation Mitsubishi Training


Module 01: - Mitsubishi PLC iQF Series Panel Wiring
Module 02: - Mitsubishi Software GX-Works3
Module 03: - Mitsubishi HMI GS2107 GT Designer3 Training
Module 04: - Mitsubishi VFD E840 FR-Configurator 2
Module 05: - Mitsubishi Networking: - Modbus RTU, Modbus TCP/IP Ethernet IP & CC-Link IE basic
Module 06:- Third Party Communication on Modbus RS485 to VFD, Energy Meter, PID, Analog Signal
Time Duration 3 Months Daily Monday to Friday 4 hours Training Fee 20000 INR
Why Mitsubishi Training of Softwell?
Transform Your Career with Comprehensive, Hands-On Training
Modules Covered:
Mitsubishi PLC FX 5U / iQF Series: Industry 4.0 ready; transition from older CPUs; GX Works3 exclusive support.
Mitsubishi HMI 2107 WTBD N: HMI configuration, UI design, PLC integration.
Mitsubishi VFD FR E840: VFD setup, configuration, energy-efficient control.
Mitsubishi Networking: Modbus RTU, CC-Link IE, Modbus TCP protocols.
Third-Party Instrument Interfacing: RS485 interfacing with VFD, PID, Energy Meter.
PLC Panel Wiring: Hands-on wiring, safety, and panel design.
Special Features:
Industry-Recognized Certification: Validate your Mitsubishi automation skills.
Real-World Projects: Apply knowledge to practical, industry-based projects.
Flexible Learning Options:
Weekend Classes: Designed for working professionals.
Recorded Sessions: Review or catch up on missed content.
Job Placement Support:
Resume Building Workshops
Interview Preparation Sessions
Job Placement Assistance
Expert Lectures:
Insights from industry experts on the latest automation trends and technologies.
Mitsubishi PLC iQF Course Contents
Introduction to Mitsubishi iQF / FX5U PLC Series: Overview of features, architecture, and industrial automation applications.
Understanding GX Works3 Software: In-depth exploration of the GX Works3 interface, tools, and capabilities.
Project Creation and Management: How to create, manage, and organize PLC projects in GX Works3.
Programming Languages: Instruction in ladder logic, structured text, and function block diagram programming within GX Works3.
Basic Instructions: Introduction to fundamental PLC instructions and their applications.
Timer and Counter Instructions: Using timers and counters for managing time-based and count-based operations.
Math and Arithmetic Instructions: Performing mathematical and arithmetic operations within PLC programs.
Comparison and Data Handling Instructions: Comparing values and handling data for decision-making and processing.
Data Registers and Memory Areas: Managing data registers and memory areas for storing and accessing data.
Analog I/O and PID Control: Configuring analog inputs/outputs and implementing PID control for precise process control.
Advanced Programming Techniques: Utilizing advanced instructions, data handling, and processing functions.
I/O Configuration and Mapping: Setting up and managing input/output points for seamless hardware integration.
Input Mapping: Detailed configuration and mapping of inputs to PLC logic for accurate system operation.
Output Mapping: Mapping outputs to control devices, ensuring proper execution of control commands.
Alarm Mapping: Configuring and managing alarm signals within the PLC for effective monitoring and response.
Network Configuration: Configuring CC-Link IE, Ethernet, and Modbus protocols for communication between devices.
Network Mapping: Setting up and managing network communications, including mapping devices across the network.
Project Development 5000 Networks: Developing complex projects involving 5000 networks for large-scale automation systems.
Creating and Using Function Blocks: Development and implementation of reusable function blocks in PLC programming.
Motion Control: Introduction to motion control functions for robotics and servo applications.
Tower Mapping: Configuring tower lights for visual indication of machine status and alarms.
System Backup and Restore: Best practices for backing up and restoring PLC projects and configurations.
Security Features: Implementing security measures in GX Works3 to protect PLC programs and configurations.
Firmware Updates: Managing and applying firmware updates to ensure optimal PLC performance.
Real-Time Clock (RTC) Setup: Configuring the RTC for time-based operations and logging.
Integration with Third-Party Devices: Connecting and communicating with non-Mitsubishi devices via RS485, Modbus, etc.
Data Logging and Monitoring: Setting up data logging, monitoring, and alarms for real-time system management.
Simulation and Testing: Using GX Works3’s simulation tools to test and validate PLC programs before deployment.
Troubleshooting and Debugging: Techniques for identifying and resolving issues in PLC programs.
Expert Lectures and Industry Insights: Learning from industry experts about the latest trends and technologies in automation.
Mitsubishi HMI GT Desiner3 Course Contents
Introduction to Mitsubishi HMI GT Designer3: Overview of the software, its interface, and its role in HMI development.
Getting Started with GT Designer3: Basic setup, installation, and initial configuration of the GT Designer3 environment.
Project Creation: How to create and manage new HMI projects within GT Designer3.
Screen Design Basics: Designing and configuring screens using GT Designer3's graphical tools.
Graphic Elements: Utilizing various graphic elements such as buttons, indicators, and gauges.
Object Properties: Setting and managing properties for HMI objects to control their behavior and appearance.
Data Registration and Mapping: Registering and mapping data points from the PLC to HMI objects.
Creating and Using Tags: Defining and using tags for dynamic data representation and interaction.
Screen Navigation: Designing and implementing screen navigation for a smooth user experience.
Alarm and Event Management: Configuring alarm displays and event logging for real-time monitoring.
Trend and Data Logging: Setting up and displaying trend graphs and data logs for historical analysis.
Recipe Management: Creating and managing recipes for automated data handling and process control.
User Access and Security: Implementing user authentication and access levels to secure HMI operations.
Script Programming: Writing and integrating scripts to enhance HMI functionality and interactivity.
Communication Setup: Configuring communication settings to interface with Mitsubishi PLCs and other devices.
Simulation and Testing: Using the simulation features to test and validate HMI designs before deployment.
HMI to PLC Data Exchange: Handling data exchange between HMI and PLC, including read/write operations.
Graphics and Animation: Adding animations and advanced graphics to improve visual appeal and functionality.
Troubleshooting and Debugging: Techniques for identifying and fixing issues within GT Designer3 projects.
Best Practices and Optimization: Tips for optimizing HMI designs for performance, usability, and maintainability.
Mitsubishi VFD FR-Configurator2 Course Contents
Introduction to Mitsubishi VFD FR-Configurator 2: Overview of the software’s features and benefits for configuring VFDs.
Getting Started: Initial setup and installation of FR-Configurator 2.
User Interface Navigation: Understanding the layout and key functions of the FR-Configurator 2 interface.
Device Connection: How to connect and communicate with Mitsubishi VFDs using FR-Configurator 2.
Basic Configuration: Setting up basic parameters for Mitsubishi VFDs, including motor settings and operational modes.
Advanced Parameter Settings: Configuring advanced parameters for optimized VFD performance, including acceleration, deceleration, and frequency settings.
PID Control Setup: Implementing PID control for precise speed and torque regulation.
Communication Settings: Configuring communication protocols such as Modbus, CC-Link, and Ethernet.
Program Creation: Creating and managing user-defined programs for specialized applications.
Data Logging and Monitoring: Setting up data logging and real-time monitoring of VFD performance and status.
Fault Diagnosis and Troubleshooting: Identifying and resolving common issues and faults using FR-Configurator 2.
Parameter Backup and Restore: Techniques for backing up and restoring VFD configuration settings.
Firmware Updates: Updating VFD firmware to ensure compatibility and performance improvements.
Integration with PLCs: Configuring VFDs to work seamlessly with Mitsubishi and third-party PLCs.
Energy Savings and Efficiency: Implementing settings for energy savings and enhanced efficiency in VFD operation.
Custom Function Blocks: Creating and applying custom function blocks for specialized VFD control.
Multi-Drive Systems: Configuring and managing multiple VFDs in a single system using FR-Configurator 2.
Safety Features: Configuring safety parameters and functions to ensure safe operation of VFDs.
User Management: Setting up user permissions and access levels for FR-Configurator 2.
Real-World Applications: Practical examples and case studies of VFD configuration for various industrial applications
YouTube Channel of Mitsubishi PLC Training

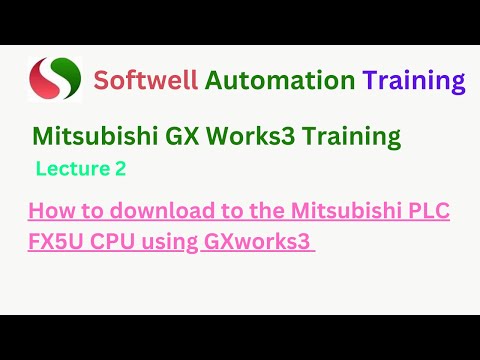
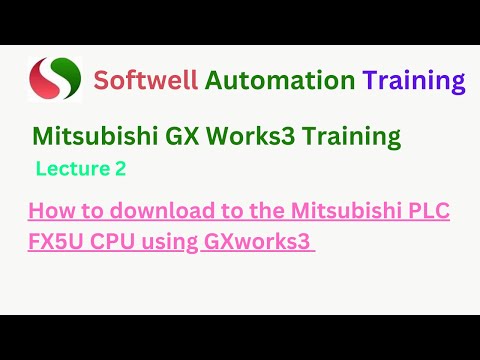
Pune Location
Office No 55, Kunal plaza, 4th floor, old Mumbai Pune Highway, Chinchwad railway Station Pune 411019
Contacts
Mrs. Ritu Pawar Mob +91-7420804059
pune@softwellautomation.com
Head Office
Enquiry Form for Industrial Automation Training
Branch Office
Contacts
Mrs. Ritu Pawar Mob +91-9909700584
noida@softwellautomation.com
Noida Location
Block B. Sector 02 NOIDA 201301