Contact US 🤙+91-990970058, 🤙🤙+91-7420804059 🇮🇳 ✉️info@softwellautomation.com
Rockwell PLC HMI SCADA VFD Networking Training


Module 01: - Allen Bradley PLC MicroLogix 1400 , Software RSLogix 500 V12.0
Module 02: - Allen Bradley PLC CompactLogix 5371 Old Software RSLogix 5000 V20.05
Module 03: - Allen Bradley PLC CompactLogix 5371 , New Software Studio 5000 V35.0
Module 04: - Allen Bradley HMI FactoryTalk Machine Edition
Module 05: - Allen Bradley SCADA FactoryTalk Machine Edition
Module 06: - Allen Bradley VFD PowerFlex 525E Ethernet port
Module 07: - Allen Bradley Networking: - Modbus RTU, EtherNet IP, Modbus TCP/IP
Module 08:- Allen Bradley PLC Panel Wiring
Training Fee 25000 INR Time Duration 3 Months Time 4 hrs Mon - Fri
Allen Bradley PLC RSLogix 500 Training Course Contents
Introduction to PLCs and RSLogix 500:
Basics of programmable logic controllers and industrial automation.
Overview of Allen-Bradley PLCs and RSLogix 500 software.
Hardware Overview:
Introduction to Allen-Bradley PLC hardware, including MicroLogix series.
Overview of input/output modules, communication options, and wiring.
Software Installation and Project Setup:
Installing and setting up the RSLogix 500 software.
Creating and managing projects.
Ladder Logic Programming:
Introduction to ladder logic programming language.
Creating ladder logic programs for basic control tasks.
Digital and Analog I/O Programming:
Configuring and programming digital input and output devices.
Working with analog signals and modules.
Timers and Counters:
Understanding timer and counter instructions.
Incorporating timers and counters into control logic.
Bitwise Logic and Shift Registers:
Using bitwise instructions for more complex logic.
Implementing shift registers for sequential control.
Math Instructions and Data Handling:
Utilizing math instructions for calculations.
Data manipulation and conversion instructions.
Subroutines and Program Organization:
Creating and using subroutines for modular programming.
Organizing and structuring programs for clarity and maintainability.
Advanced Instructions:
Introduction to advanced instructions like compare, move, and logical operations.
Utilizing jump and branch instructions.
HMI Integration (Optional):
Basic overview of integrating Human Machine Interfaces (HMIs) with RSLogix 500 projects.
Troubleshooting and Debugging:
Techniques for diagnosing and resolving programming issues.
Using online monitoring and diagnostic tools.
Networking and Communication:
Basics of PLC networking and communication.
Configuring communication between PLCs and other devices.
Data Logging and Reporting (Optional):
Introduction to data logging and creating basic reports within RSLogix 500.
Project Deployment and Backup:
Downloading programs to PLCs and updating firmware.
Backing up and restoring project data.
Best Practices and Tips:
Industry best practices for efficient and effective programming.
Tips for optimizing code performance and organization.
Real-World Applications and Case Studies:
Applying learned concepts to practical industrial scenarios.
Analyzing real-world case studies to understand different control strategies.
Allen Bradley PLC RSLogix 5000 / Studio 5000 Training Course Contents
Introduction to PLCs and Control Systems:
Basics of programmable logic controllers (PLCs) and industrial control systems.
Overview of Rockwell Automation products and the Studio 5000 software suite.
Studio 5000 Logix Designer Interface:
Introduction to the Studio 5000 software environment.
Navigating the project workspace and interface elements.
Hardware Configuration:
Configuring hardware components such as PLCs, input/output modules, communication modules, and more.
Configuring and setting up network communication.
Creating and Editing Projects:
Creating new projects and importing existing ones.
Organizing projects, routines, and tasks for efficient programming.
Ladder Logic Programming:
Understanding ladder logic programming concepts.
Creating and editing ladder logic routines to control various processes.
Function Block Diagram (FBD) Programming:
Introduction to FBD programming language.
Creating and using function block diagrams for logic control.
Structured Text (ST) Programming:
Basics of structured text programming language.
Writing ST code for complex control and calculations.
Program Documentation and Comments:
Adding comments and documentation to improve program readability.
Using tag descriptions and user-defined data types.
Advanced Programming Concepts:
User-defined data types (UDTs) and structures.
Math instructions, data manipulation, and advanced functions.
Motion Control and Drive Integration:
Introducing motion control concepts.
Configuring and programming motion control in Studio 5000.
HMI and SCADA Integration (Optional):
Integrating Human Machine Interfaces (HMIs) and Supervisory Control and Data Acquisition (SCADA) systems with Studio 5000 projects.
Troubleshooting and Debugging:
Methods for diagnosing and resolving programming issues.
Using online monitoring and diagnostic tools.
Safety and Security:
Introduction to safety functions and safety-related programming.
Implementing security measures for PLC projects.
Project Deployment:
Downloading programs to PLCs and updating firmware.
Backup and restore procedures for project data.
Best Practices and Tips:
Industry best practices for efficient and maintainable programming.
Tips for optimizing code performance.
Real-World Applications and Case Studies:
Applying learned concepts to practical industrial scenarios.
Analyzing real-world case studies to understand different control strategies.
Rockwell HMI Factory talk Machin edition Course Content
Introduction to HMI and FactoryTalk View ME:
Basics of Human Machine Interface (HMI) systems and their importance in industrial automation.
Overview of Rockwell Automation's FactoryTalk View ME software.
HMI Hardware and Communication Setup:
Introduction to HMI hardware components and models.
Configuring communication between HMI and PLCs/Controllers.
FactoryTalk View ME Interface:
Navigating the FactoryTalk View ME software interface.
Introduction to project creation and management.
Creating and Configuring Graphic Displays:
Building graphic screens with interactive elements.
Adding buttons, indicators, trends, and other visual elements.
Working with Tags and Data Connections:
Connecting HMI objects to PLC tags and variables.
Configuring data sources and addressing.
Animations and Dynamic Elements:
Creating animations and dynamic effects for better visualization.
Utilizing macros for interactive behavior.
Alarm Configuration and Handling:
Setting up alarms and events.
Configuring alarm messages and responses.
Trends and Data Logging:
Creating trend displays to visualize historical data.
Configuring data logging and historical data storage.
Security and User Management:
Implementing user authentication and role-based access.
Configuring security settings for HMI applications.
Recipe Management (Optional):
Introduction to recipe management and usage.
Creating and using recipes for process control.
Multi-Language Support:
Implementing multi-language support in HMI applications.
Creating applications that can be displayed in different languages.
Advanced Graphics and Navigation:
Creating complex graphics with layered displays.
Implementing navigation buttons and menus.
HMI Scripting and Macros:
Introduction to scripting for enhanced functionality.
Creating macros to execute custom actions.
Remote Access and Web Servers (Optional):
Enabling remote access to HMI applications.
Configuring web servers for remote monitoring.
Troubleshooting and Debugging:
Diagnosing issues and errors in HMI applications.
Using diagnostic tools and techniques.
Project Deployment and Backup:
Deploying HMI applications to target devices.
Backing up and restoring HMI projects.
Best Practices and Design Guidelines:
Design considerations for creating user-friendly and efficient HMI applications.
Tips for optimizing performance and user experience.
Real-World Applications and Case Studies:
Applying learned concepts to practical industrial scenarios.
Analyzing real-world case studies to design effective HMI applications.
Rockwell Allen Bradely VFD Course Content
Introduction to Variable Frequency Drives (VFDs):
Understanding the basic principles of VFDs and their role in motor control.
Differentiating between VFDs and traditional motor starters.
Overview of PowerFlex 525E Drive:
Introduction to the PowerFlex 525E drive and its features.
Understanding the applications and industries where the drive is commonly used.
Hardware and Installation:
Exploring the physical components of the PowerFlex 525E drive.
Guidelines for proper installation, wiring, and grounding.
Drive Configuration and Setup:
Navigating the drive's control panel and keypad.
Basic parameter setup and configuration for motor control.
Programming and Control:
Understanding parameter groups and their significance.
Configuring speed control, acceleration, deceleration, and other control settings.
Start-up and Commissioning:
Step-by-step procedure for starting up the drive for the first time.
Troubleshooting common start-up issues.
Control Modes and Applications:
Exploring different control modes such as V/Hz, Sensorless Vector, and Closed-Loop Vector.
Understanding how to select the appropriate control mode for different applications.
Advanced Programming and Features:
Working with more advanced parameters and features.
Implementing features like PID control, brake control, and custom logic.
Communication and Networking:
Setting up communication interfaces such as Ethernet/IP, Modbus, etc.
Integrating the PowerFlex drive into a larger automation system.
Troubleshooting and Diagnostics:
Interpreting fault codes and diagnosing drive issues.
Utilizing built-in diagnostics tools for effective troubleshooting.
Energy Savings and Optimization:
Exploring energy-efficient features and strategies.
Implementing energy monitoring and optimization techniques.
Maintenance and Safety:
Proper maintenance practices to ensure the longevity of the drive.
Safety considerations when working with VFDs.
Hands-on Labs and Practical Exercises:
Hands-on exercises to reinforce theoretical concepts.
Simulating real-world scenarios using the PowerFlex 525E drive.
Case Studies and Application Examples:
Analyzing real-world applications where the PowerFlex 525E drive is used.
Understanding the drive's role in improving efficiency and productivity.
Rockwell Allen Bradley PLC to VFD Networking Course Content
A course on Allen Bradley PLC (Programmable Logic Controller) and VFD (Variable Frequency Drive) networking would typically cover a range of topics related to industrial automation, control systems, and networking. Here's a general outline of what such a course might include:
Module 1: Introduction to PLCs and VFDs
Overview of industrial automation and control systems
Introduction to PLCs and their role in automation
Introduction to VFDs and their role in motor control
Advantages of integrating PLCs and VFDs in industrial processes
Module 2: Allen Bradley PLC Basics
Introduction to Allen Bradley PLCs and their product lines
Hardware components of an Allen Bradley PLC system
PLC programming languages (Ladder Logic, Structured Text, etc.)
Basics of programming using Allen Bradley's RSLogix or Studio 5000 software
Module 3: VFD Fundamentals
Introduction to Variable Frequency Drives (VFDs)
VFD components and operation
Basic motor control using VFDs
Setting up and configuring VFD parameters
Module 4: PLC-VFD Integration
Understanding the communication protocols used for PLC-VFD communication (e.g., Modbus, EtherNet/IP)
Wiring and hardware considerations for connecting PLCs and VFDs
Configuring communication settings in PLC and VFD programming software
Module 5: Networking Concepts for Automation
Introduction to industrial networking protocols (Ethernet, Profibus, DeviceNet, etc.)
Network topologies and architectures
Network addressing, subnetting, and IP configurations
Network security and best practices in industrial environments
Module 6: Ethernet/IP for PLC-VFD Communication
Overview of Ethernet/IP protocol for industrial communication
Setting up Ethernet/IP communication between Allen Bradley PLCs and VFDs
Data exchange between PLC and VFD using Ethernet/IP
Module 7: Troubleshooting and Diagnostics
Troubleshooting common issues in PLC-VFD communication
Using diagnostic tools and software for debugging
Methods for identifying and resolving network-related problems
Module 8: Case Studies and Hands-on Labs
Real-world examples of PLC-VFD integration in different industries
Hands-on exercises for programming, configuring, and troubleshooting PLCs and VFDs
Simulation of communication scenarios using software tools
Module 9: Advanced Topics
Advanced programming techniques for PLCs and VFDs
Redundancy and fault-tolerance in PLC-VFD systems
Remote monitoring and control of PLC-VFD systems
Integration with SCADA (Supervisory Control and Data Acquisition) systems
Module 10: Future Trends and Industry Applications
Emerging trends in industrial automation and control
Industry 4.0 concepts and their impact on PLC-VFD networks
Case studies of innovative applications in different sectors
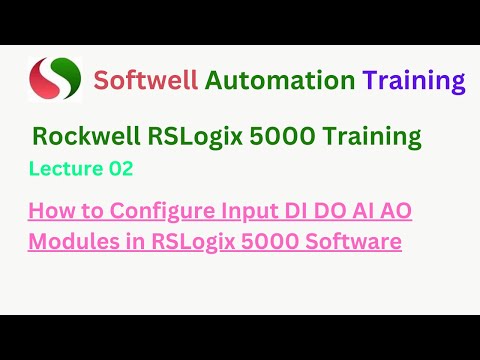
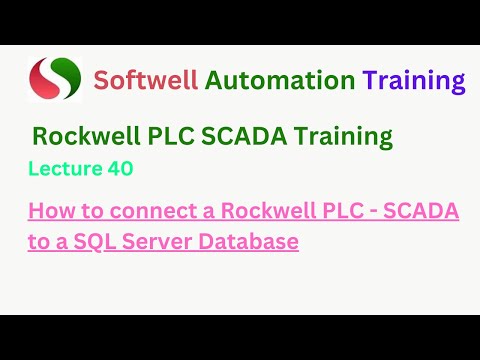
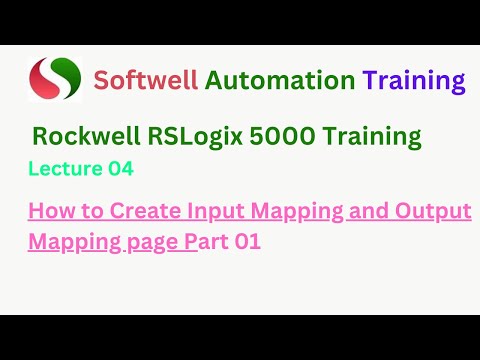
Pune Location
Office No 55, Kunal plaza, 4th floor, old Mumbai Pune Highway, Chinchwad railway Station Pune 411019
Contacts
Mrs. Ritu Pawar Mob +91-7420804059
pune@softwellautomation.com
Head Office
Enquiry Form for Industrial Automation Training
Branch Office
Contacts
Mrs. Ritu Pawar Mob +91-9909700584
noida@softwellautomation.com
Noida Location
Block B. Sector 02 NOIDA 201301