ABB PLC VFD Networking Training
Why ABB PLC HMI VFD Training of Softwell?
ABB PLC Training Codesys
Learn ABB PLC programming with specialized Codesys training, focusing on industrial automation, advanced control systems, and hands-on experience
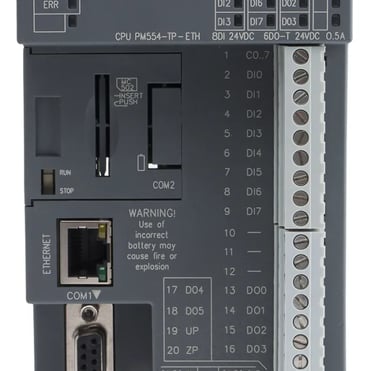
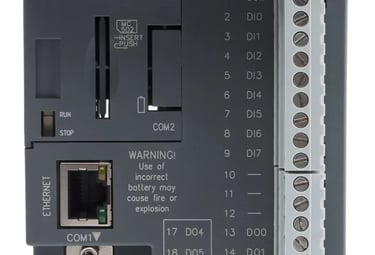
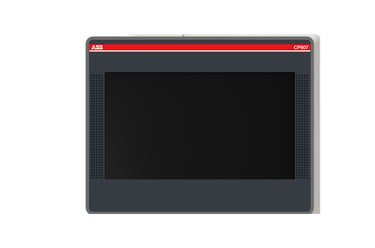
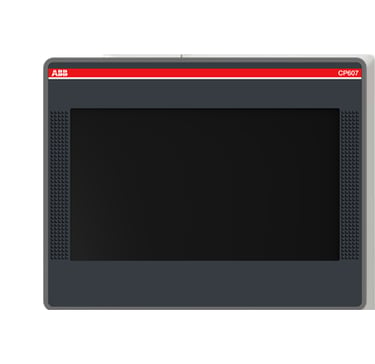
ABB HMI CP607 Training
ABB CP607: Advanced HMI offering seamless control, intuitive interface, robust design, and real-time monitoring for industrial automation solutions.
ABB VFD ACS 580 Training
ABB Drive Composer Entry Software Training for Vector Control & Scalaer Control Drive with Modbus RTU, Modbus TCP, ProfiNet, Ethernet IP
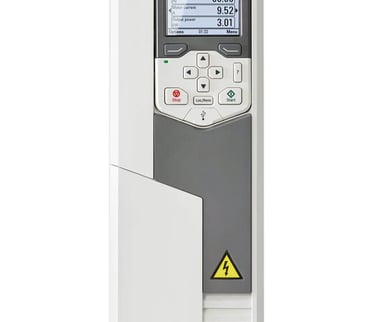
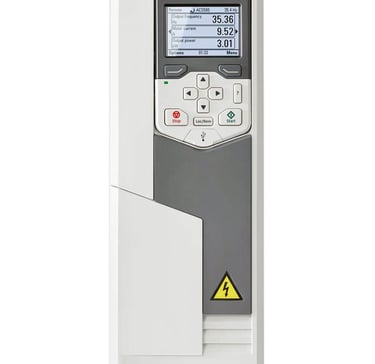
Project Development
Melsec ABB PLC Programming for Automotive and Process Industries Aligned with Global Standards of 5000 Network Logic
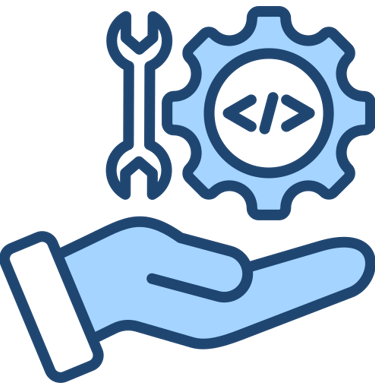
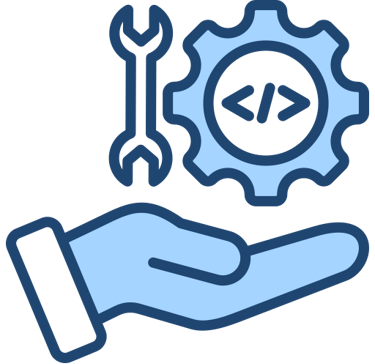
ABB PLC Codesys Software Course Content
Introduction to ABB Codesys PLC Series:
Overview of features, architecture, and industrial automation applications.Understanding Codesys Development Environment:
In-depth exploration of the Codesys IDE interface, tools, and capabilities.Project Creation and Management:
How to create, manage, and organize PLC projects within the Codesys environment.Programming Languages:
Instruction in IEC 61131-3 languages such as ladder logic, structured text, and function block diagram programming within Codesys.Basic Instructions:
Introduction to fundamental PLC instructions and their applications.Timer and Counter Instructions:
Using timers and counters for managing time-based and count-based operations.Math and Arithmetic Instructions:
Performing mathematical and arithmetic operations within PLC programs.Comparison and Data Handling Instructions:
Comparing values and handling data for decision-making and processing.Data Registers and Memory Areas:
Managing data registers and memory areas for storing and accessing data.Analog I/O and PID Control:
Configuring analog inputs/outputs and implementing PID control for precise process management.Advanced Programming Techniques:
Utilizing advanced instructions, data handling, and processing functions.I/O Configuration and Mapping:
Setting up and managing input/output points for seamless hardware integration.Input Mapping: Detailed configuration and mapping of inputs to PLC logic for accurate system operation.
Output Mapping: Mapping outputs to control devices, ensuring proper execution of control commands.
Alarm Mapping: Configuring and managing alarm signals within the PLC for effective monitoring and response.
Network Configuration:
Configuring Ethernet/IP, Modbus, and OPC UA protocols for communication between devices.Network Mapping:
Setting up and managing network communications, including mapping devices across the network.Project Development for Large-Scale Systems:
Developing complex projects involving extensive networks for industrial automation.Creating and Using Function Blocks:
Development and implementation of reusable function blocks in Codesys programming.System Backup and Restore:
Best practices for backing up and restoring PLC projects and configurations.Security Features:
Implementing security measures in Codesys to protect PLC programs and configurations.Firmware Updates:
Managing and applying firmware updates to ensure optimal PLC performance.Real-Time Clock (RTC) Setup:
Configuring the RTC for time-based operations and logging.Integration with Third-Party Devices:
Connecting and communicating with non-ABB devices via Modbus, Ethernet/IP, etc.Data Logging and Monitoring:
Setting up data logging, monitoring, and alarms for real-time system management.Simulation and Testing:
Using Codesys’s simulation tools to test and validate PLC programs before deployment.Troubleshooting and Debugging:
Techniques for identifying and resolving issues in PLC programs.
ABB HMI CP607 Control Builder Course Content
Introduction to ABB CP607: Overview of ABB CP607 HMI, its role in industrial automation, and how it enhances control and monitoring.
HMI Basics: Understand Human-Machine Interface (HMI) fundamentals, including its purpose, design principles, and application in industrial systems.
ABB CP607 Overview: Detailed look at the features and specifications of the ABB CP607 HMI, including screen size, resolution, and input options.
Control and Monitoring: Learn how CP607 enables seamless control and real-time monitoring of machinery, equipment, and industrial processes.
User Interface Design: Explore the interface design of CP607, focusing on intuitive navigation, icons, widgets, and customization for different user needs.
Touchscreen Operation: Master touchscreen functionality, including gestures, multi-touch capabilities, and configuring touch-based controls for ease of use.
Creating and Managing Projects: Learn how to create, edit, and manage HMI projects using the ABB PC-based engineering tools and software.
Communication Protocols: Understand communication between the CP607 and other devices using protocols like Modbus, Profibus, Profinet, and Ethernet/IP.
Configuring Tags and Variables: Learn how to configure and manage variables, including defining tags for real-time data monitoring and control.
Alarm and Event Management: Set up alarms, notifications, and event logs on CP607 for critical monitoring and alerting during system operation.
Data Logging and Trending: Study how to log data over time, visualize trends, and generate reports for analysis and decision-making.
Screen Layout Design: Understand how to design efficient and user-friendly screen layouts for displaying key system parameters and information.
Animations and Graphics: Explore creating dynamic animations and graphical representations of real-time data for enhanced visualization and user interaction.
Security Features: Learn about user access control, password protection, and securing HMI screens to prevent unauthorized access and ensure system integrity.
Multi-language Support: Configure CP607 for multiple languages, enabling localized user interfaces for global use in different regions and industries.
Integrating with PLCs: Understand how to integrate ABB CP607 with PLCs, including data exchange, control commands, and status monitoring.
Diagnostic and Troubleshooting Tools: Learn to use diagnostic features for troubleshooting communication issues, system errors, and device malfunctions.
Firmware Updates: Study how to update the CP607 firmware, ensuring the HMI operates with the latest features and bug fixes.
Customizing Screens: Learn how to customize HMI screens, including background images, logos, and user-defined buttons for personalized control.
Final Evaluation and Certification: Review key concepts from the training, complete practical exercises, and earn certification upon successful course completion.
ABB VFD ACS580 Drive Composer Pro Software Course Content
Introduction to VFD technology: Learn the basics of Variable Frequency Drive, its purpose in motor speed regulation, energy efficiency, and cost-saving applications.
Working principle of VFD: Understand how VFDs control motor speed by varying the frequency of the power supplied to the motor.
Components of VFD system: Study the key components, including the power section, control section, cooling fans, and user interface for operation.
ACS580 and ACS880 features: Get familiar with the ACS580’s user-friendly design and the ACS880’s advanced features for higher performance and precision.
Differences between ACS580 and ACS880: Understand the key distinctions, where ACS580 is standard for basic needs, while ACS880 provides enhanced performance and control.
VFD control methods: Learn about Volts/Hz control for simplicity and Vector control for better precision in motor torque and speed management.
Advanced control methods: Explore advanced methods like sensorless vector control and closed-loop feedback systems to achieve more precise motor control.
PID control for motor regulation: Understand how Proportional-Integral-Derivative (PID) control manages motor speed, torque, and system performance in variable-speed applications.
Electrical wiring and connections: Study how to properly wire the VFD to the motor, power supply, and control devices, ensuring safety and reliability.
Safety considerations during installation: Learn essential safety procedures, including lock-out/tag-out (LOTO), proper grounding, and ensuring electrical and mechanical safety during installation.
Using ACS580/880 keypad: Gain proficiency in navigating the ACS580/880 keypad for configuring parameters, setting motor speeds, and adjusting drive settings.
Programming VFD parameters: Learn to modify various drive parameters, including speed limits, acceleration/deceleration rates, and motor protection features using the keypad.
ABB Drive Composer software: Understand how to use Drive Composer for more advanced configurations, diagnostics, and firmware updates for the VFD.
Setting up communication protocols: Learn how to configure communication protocols like Modbus RTU, Profibus, and Profinet to integrate the VFD into automated systems.
Connecting VFD to SCADA: Understand the process of connecting the ACS580/880 to SCADA systems for remote control, monitoring, and data collection.
Troubleshooting common faults: Learn how to interpret fault codes, diagnose motor or drive issues, and resolve common problems with ACS580/880 drives.
Preventive maintenance practices: Study recommended maintenance procedures, including inspecting components, cleaning cooling fans, and checking electrical connections to ensure VFD longevity.
Firmware updates via Drive Composer: Learn to update the firmware of ACS580/880 using Drive Composer software to enhance functionality and correct performance issues.
Optimizing VFD performance: Discover techniques for fine-tuning the ACS580/880 to improve energy efficiency, reduce wear and tear, and extend motor life.
Certification and final evaluation: Participate in a comprehensive exam to assess understanding and earn certification for successfully completing the ACS580/880 training program.
Introduction to Drive Composer Pro: Learn about the Drive Composer Pro software, designed for advanced configuration, diagnostics, and tuning of ABB VFDs.
Installation of Drive Composer Pro: Understand how to install Drive Composer Pro software on your PC and connect it to ABB VFDs for programming.
User Interface Overview: Familiarize yourself with the Drive Composer Pro interface, including layout, tools, and options for efficient configuration and diagnostics.
Creating and Modifying Drive Projects: Learn how to create and modify drive projects, storing configuration settings, parameters, and project templates for future use.
Parameter Configuration and Tuning: Use Drive Composer Pro to configure VFD parameters, fine-tune motor settings, and optimize system performance based on application needs.
Monitoring Drive Operation: Learn how to monitor drive operation in real-time, track performance metrics, and identify potential issues using Drive Composer Pro.
Fault Diagnosis and Troubleshooting: Use Drive Composer Pro’s diagnostic tools to identify faults, view error logs, and troubleshoot drive or motor-related problems.
Firmware Updates via Drive Composer Pro: Learn to perform firmware updates on ACS580/880 VFDs, improving functionality, adding features, or resolving known issues.
Backup and Restore Drive Settings: Discover how to back up VFD configurations and restore settings from backups, ensuring minimal downtime during maintenance.
Integrating with Control Systems: Learn how to integrate Drive Composer Pro with industrial control systems, enabling seamless communication for centralized monitoring and control of VFDs.
Enquiry for ABB PLC HMI VFD Training
📞 Contact Information
Mrs. Ritu Pawar
📱 Mobile: +91-7420804059
📧 Email: pune@softwellautomation.com
Mr. Bhawesh Kumar Singh
📱 Mobile: +91-9909700584
📧 Email: info@softwellautomation.com
📍 Pune Office Location
Softwell Automation
Office No. 55, 4th Floor, Kunal Plaza,
Old Mumbai-Pune Highway,
Chinchwad Railway Station, Pune – 411019
🧭 Landmark: Above RBL Bank