Rockwell PLC HMI SCADA VFD Networking Training
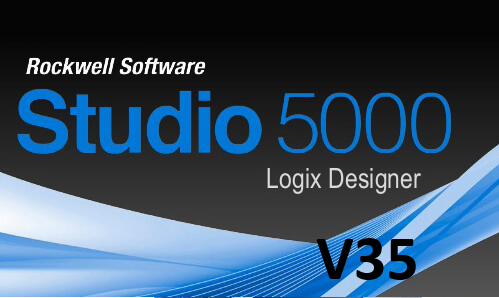
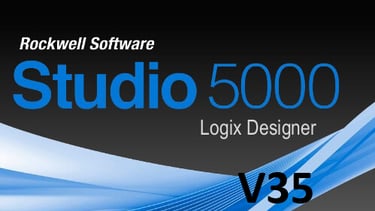
Allen-Bradley PLC, HMI, SCADA, VFD & Networking Training
Old PLC: Basic Micrologix 1400 Software RSLogix 500 |
New Advance PLC CompactLogix 5370/5380 | PLC Software: Studio 5000 V35.0
HMI: PanelView 5510, PanelView 5310 | Software: FactoryTalk View ME
VFD: PowerFlex 525 | Software: Drive Executive
SCADA Software: FactoryTalk View SE
Networking Protocols: Ethernet/IP, Modbus TCP/IP, DNP3 & OPC UA
Third Party Communication: VFD ,HMI Coomunication on Ethernet
Why Allen-Bradley Training of Softwell?
Rockwell PLC CompactLogix Studio 5000 V35
Rockwell PLC CompactLogix Studio 5000 V35 training enhances programming, troubleshooting, and safety skills, preparing professionals for advanced roles in automation and Industry 4.0 environments
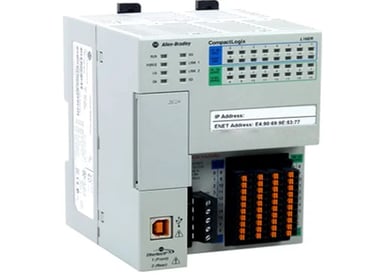
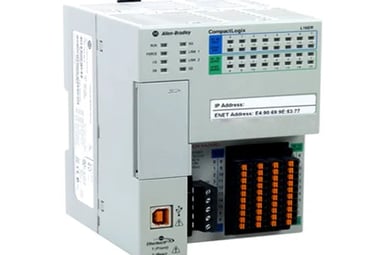
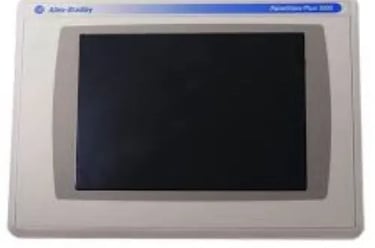
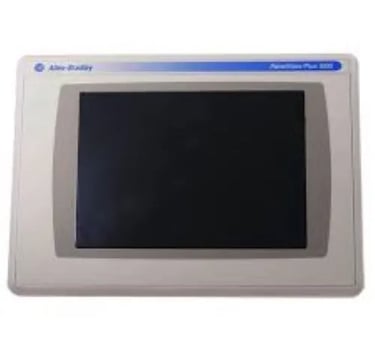
Rockwell Factorytalk Machine Edition
FactoryTalk HMI training equips professionals with skills to design, monitor, and troubleshoot industrial interfaces, improving system efficiency, reducing downtime, and enhancing operational control in automated environments essential for Industry 4.0
Rockwell SCADA Factorytalk Site Edition
FactoryTalk SCADA training enhances skills in real-time monitoring, data analysis, and system control, improving operational efficiency, reducing downtime, and preparing professionals for high-demand roles in industrial automation and process management.
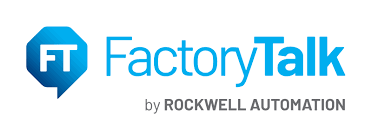
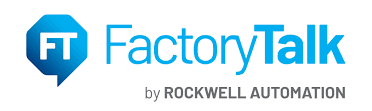
Allen Bradley Powerflex 525E Training
Allen Bradley PowerFlex VFD training provides expertise in motor control, energy efficiency, and troubleshooting, enhancing system performance, reducing downtime, and equipping professionals for advanced roles in industrial automation and process optimization.
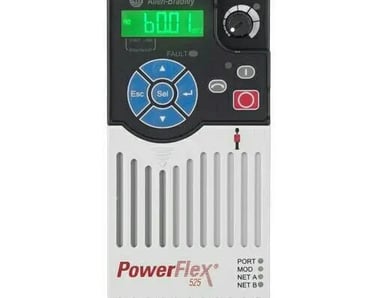
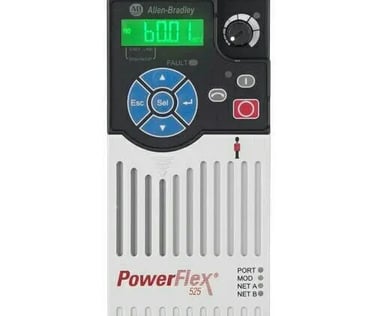
Project Development
PLC Programming for Automotive and Process Industries Aligned with Global Standards of 5000 Network Logic
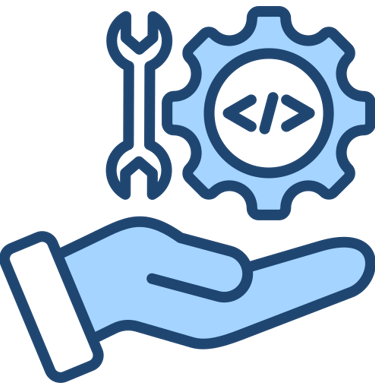
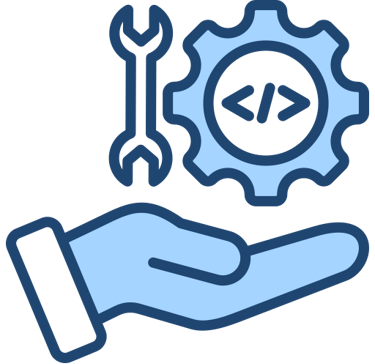
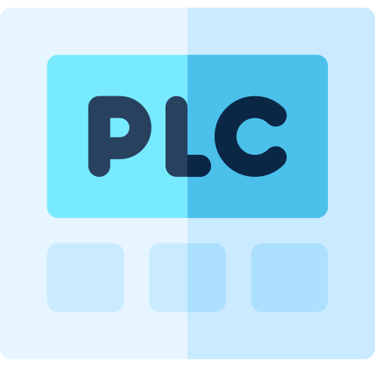
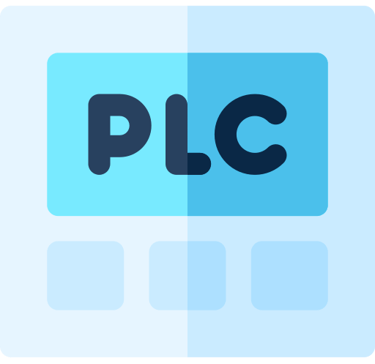
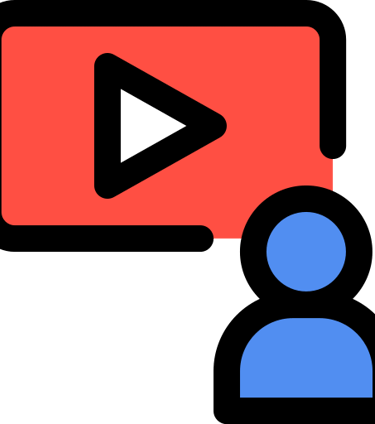
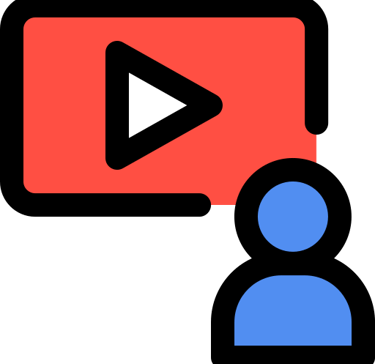
PLC Panel Wiring
Hands-On Experience with Live Panel Wiring for Real-World Automation Applications
YouTube Video of Each Tpoic
Explore 200+ Comprehensive Practice Videos on All Topics to Enhance Your Learning Experience
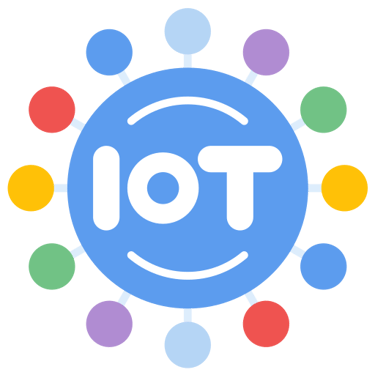
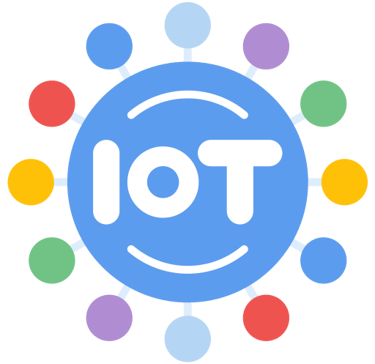
Industrial IoT
Industrial IoT Solutions with Siemens PLC: Integrating Smart Automation for the Future
Allen Bradley Studio 5000 V35 Training
Introduction to Allen Bradley CompactLogix 5370 PLC Series: Overview of features, architecture, and industrial automation applications.
Understanding Studio 5000 V35.0 Software: In-depth exploration of the Studio 5000 V35.0 interface, tools, and capabilities.
Project Creation and Management: How to create, manage, and organize PLC projects in Studio 5000 V35.0.
Programming Languages: Instruction in ladder logic programming within Studio 5000 V35.0.
Basic Instructions: Introduction to fundamental PLC instructions and their applications.
Timer and Counter Instructions: Using timers and counters for managing time-based and count-based operations.
Math and Arithmetic Instructions: Performing mathematical and arithmetic operations within PLC programs.
Comparison and Data Handling Instructions: Comparing values and handling data for decision-making and processing.
Data Files and Memory Areas: Managing data files and memory areas for storing and accessing data.
Analog I/O and PID Control: Configuring analog inputs/outputs and implementing PID control for precise process control.
Advanced Programming Techniques: Utilizing advanced instructions, data handling, and processing functions.
I/O Configuration and Mapping: Setting up and managing input/output points for seamless hardware integration.
Input Mapping: Detailed configuration and mapping of inputs to PLC logic for accurate system operation.
Output Mapping: Mapping outputs to control devices, ensuring proper execution of control commands.
Alarm Mapping: Configuring and managing alarm signals within the PLC for effective monitoring and response.
Network Configuration: Configuring protocols like Ethernet/IP and Modbus for communication between devices.
Network Mapping: Setting up and managing network communications, including mapping devices across the network.
Creating and Using Subroutines: Development and implementation of reusable subroutines in PLC programming.
Motion Control (Basic Introduction): Introduction to motion control functions for applications involving stepper motors and servos.
Tower Light Mapping: Configuring tower lights for visual indication of machine status and alarms.
System Backup and Restore: Best practices for backing up and restoring PLC projects and configurations.
Security Features: Implementing security measures in Studio 5000 V35.0 to protect PLC programs and configurations.
Firmware Updates: Managing and applying firmware updates to ensure optimal PLC performance.
Real-Time Clock (RTC) Setup: Configuring the RTC for time-based operations and logging.
Integration with Third-Party Devices: Connecting and communicating with non-Allen Bradley devices via RS485, Modbus, etc.
Data Logging and Monitoring: Setting up data logging, monitoring, and alarms for real-time system management.
Simulation and Testing: Using Studio 5000 V35.0’s simulation tools to test and validate PLC programs before deployment.
Troubleshooting and Debugging: Techniques for identifying and resolving issues in PLC programs.
Expert Lectures and Industry Insights: Learning from industry experts about the latest trends and technologies in automation.
Rockwell HMI Factory talk Machin edition Course Content
Introduction to HMI and FactoryTalk View ME: Basics of Human Machine Interface (HMI) systems and their importance in industrial automation. Overview of Rockwell Automation's FactoryTalk View ME software.
HMI Hardware and Communication Setup: Introduction to HMI hardware components and models. Configuring communication between HMI and PLCs/Controllers.
FactoryTalk View ME Interface: Navigating the FactoryTalk View ME software interface. Introduction to project creation and management.
Creating and Configuring Graphic Displays: Building graphic screens with interactive elements. Adding buttons, indicators, trends, and other visual elements.
Working with Tags and Data Connections: Connecting HMI objects to PLC tags and variables. Configuring data sources and addressing.
Animations and Dynamic Elements: Creating animations and dynamic effects for better visualization. Utilizing macros for interactive behavior.
Alarm Configuration and Handling: Setting up alarms and events. Configuring alarm messages and responses.
Trends and Data Logging: Creating trend displays to visualize historical data. Configuring data logging and historical data storage.
Security and User Management: Implementing user authentication and role-based access. Configuring security settings for HMI applications.
Recipe Management (Optional): Introduction to recipe management and usage. Creating and using recipes for process control.
Multi-Language Support: Implementing multi-language support in HMI applications. Creating applications that can be displayed in different languages.
Advanced Graphics and Navigation: Creating complex graphics with layered displays. Implementing navigation buttons and menus.
HMI Scripting and Macros: Introduction to scripting for enhanced functionality. Creating macros to execute custom actions.
Remote Access and Web Servers (Optional): Enabling remote access to HMI applications. Configuring web servers for remote monitoring.
Troubleshooting and Debugging: Diagnosing issues and errors in HMI applications. Using diagnostic tools and techniques.
Project Deployment and Backup: Deploying HMI applications to target devices. Backing up and restoring HMI projects.
Best Practices and Design Guidelines: Design considerations for creating user-friendly and efficient HMI applications. Tips for optimizing performance and user experience.
Real-World Applications and Case Studies: Applying learned concepts to practical industrial scenarios. Analyzing real-world case studies to design effective HMI applications.
Rockwell Allen Bradely VFD Course Content
Introduction to Variable Frequency Drives (VFDs): Understanding the basic principles of VFDs and their role in motor control. Differentiating between VFDs and traditional motor starters.
Overview of PowerFlex 525E Drive: Introduction to the PowerFlex 525E drive and its features. Understanding the applications and industries where the drive is commonly used.
Hardware and Installation: Exploring the physical components of the PowerFlex 525E drive. Guidelines for proper installation, wiring, and grounding.
Drive Configuration and Setup: Navigating the drive's control panel and keypad. Basic parameter setup and configuration for motor control.
Programming and Control: Understanding parameter groups and their significance. Configuring speed control, acceleration, deceleration, and other control settings.
Start-up and Commissioning: Step-by-step procedure for starting up the drive for the first time. Troubleshooting common start-up issues.
Control Modes and Applications: Exploring different control modes such as V/Hz, Sensorless Vector, and Closed-Loop Vector. Understanding how to select the appropriate control mode for different applications.
Advanced Programming and Features: Working with more advanced parameters and features. Implementing features like PID control, brake control, and custom logic.
Communication and Networking: Setting up communication interfaces such as Ethernet/IP, Modbus, etc. Integrating the PowerFlex drive into a larger automation system.
Troubleshooting and Diagnostics: Interpreting fault codes and diagnosing drive issues. Utilizing built-in diagnostics tools for effective troubleshooting.
Energy Savings and Optimization: Exploring energy-efficient features and strategies. Implementing energy monitoring and optimization techniques.
Maintenance and Safety: Proper maintenance practices to ensure the longevity of the drive. Safety considerations when working with VFDs.
Hands-on Labs and Practical Exercises: Hands-on exercises to reinforce theoretical concepts. Simulating real-world scenarios using the PowerFlex 525E drive.
Case Studies and Application Examples: Analyzing real-world applications where the PowerFlex 525E drive is used. Understanding the drive's role in improving efficiency and productivity.
Rockwell Allen Bradley Networking Course Content
PLC to PLC Communication: Exploring PLC-to-PLC communication scenarios, various protocols like Ethernet IP, and hands-on exercises for effective data exchange.
PLC to VFD on Modbus RTU: Understanding Modbus RTU for PLC-to-VFD communication, including configuration, addressing, data mapping, and practical exercises for setup.
PLC to Energy Meter Communication: Understanding communication with energy meters, common protocols like Modbus, configuring data exchange with PLCs, and practical hands-on exercises.
PLC to VFD on Ethernet IP: Introduction to Ethernet IP protocol for VFDs, configuring PLC-to-VFD communication, setting up parameters, and hands-on exercises for control.
PLC to Remote IO on Ethernet IP: Configuring communication between PLCs and remote I/O devices using Ethernet IP, including setup, addressing, and hands-on exercises.
MicroLogix PLC to CompactLogix on Ethernet IP: Configuring Ethernet IP communication between MicroLogix PLC to CompactLogix, including setup, addressing, and practical exercises for integration.
PLC to Mobile Interfacing: Configuring PLC communication with mobile devices, including mobile app integration, data exchange, and hands-on exercises for real-time control.
PLC to Web Page Interfacing: Integrating PLCs with web pages for remote monitoring and control, including configuration, data exchange, and hands-on exercises for setup.
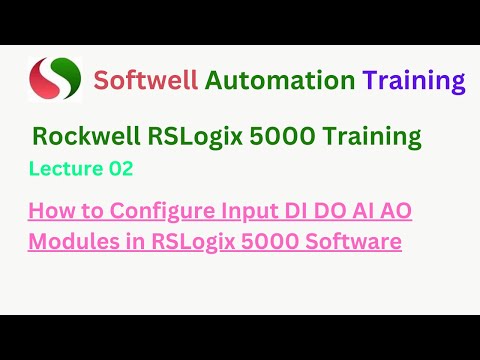
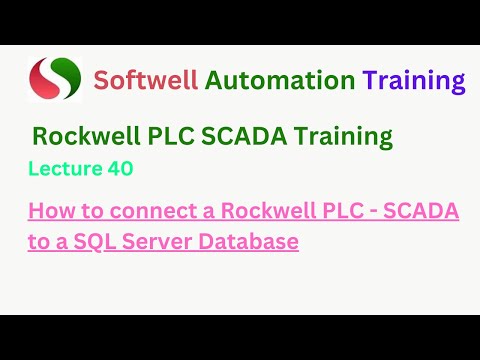
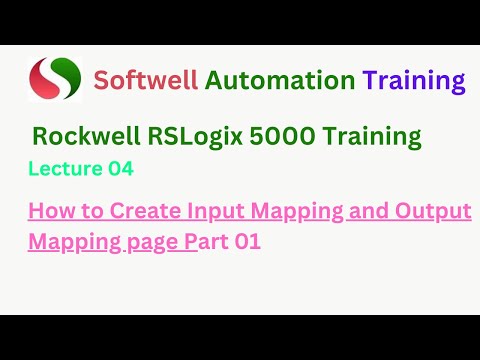
📞 Contact Information
Mrs. Ritu Pawar
📱 Mobile: +91-7420804059
📧 Email: pune@softwellautomation.com
Mr. Bhawesh Kumar Singh
📱 Mobile: +91-9909700584
📧 Email: info@softwellautomation.com
📍 Pune Office Location
Softwell Automation
Office No. 55, 4th Floor, Kunal Plaza,
Old Mumbai-Pune Highway,
Chinchwad Railway Station, Pune – 411019
🧭 Landmark: Above RBL Bank